Again in 2017, world enterprise Deloitte printed a report about improvements in industrial actual property (CRE), which listed “5 themes that CRE house owners ought to take into account integral to their enterprise technique.” A kind of themes was 3D printing. Now, it appears that evidently additive building (AC) might lastly be making its mark within the CRE sector. In one of many largest 3D printed CRE tasks in U.S. historical past, American retail large Walmart has added an 8,000-square-foot enlargement to its Supercenter location in Athens, Tennessee. The corporate was intrigued by AC know-how, which is commonly showcased as a possible savior for the nation’s housing scarcity, and wished to see if it might actually be used to construct the enlargement extra shortly and with decrease prices.
“Walmart is all the time trying to innovate and leverage growing applied sciences, and as we dug deeper into the alternatives inside 3-D concrete printing, we determined it was a path price exploring,” stated Mike Neill, Walmart, Vice President for U.S. Development.
The Athens enlargement isn’t a retail retailer—as a substitute, it’s a spot to carry gadgets bought on-line by clients earlier than they’re delivered or picked up. The multinational company is at the moment planning to construct greater than 200 different additions like this, so time- and cost-saving efforts are essential issues.
Walmart employed AC agency Alquist 3D to construct the Athens enlargement with its 3D concrete printing (3DCP) robotic know-how. The younger firm, which moved to Colorado final yr, has loads of expertise within the housing market, constructing 3D printed properties by itself and with Habitat for Humanity in Virginia. The three Habitat homes function monitoring programs, which had been put in by researchers at Virginia Tech. Janet V. Inexperienced, CEO of Habitat for Humanity Peninsula and Better Williamsburg, says that by way of indoor environmental high quality, gases, and humidity, the sensors present that the 3D printed properties are performing higher than historically constructed homes.
Nonetheless, a undertaking to 3D print properties in Iowa final yr didn’t go fairly as nicely. The corporate tried out a number of supply programs and supplies to print the outside partitions of the primary home in a deliberate growth of 10, however the construction was torn down after superficial cracks occurred.
“That scenario I believe uncovered the issue that 3-D building printing is at right this moment. There are problems round temperature, humidity, water, all types of environmental components,” defined Pete Evans, an assistant professor in industrial design at undertaking accomplice Iowa State College.

3D printing builds issues by layering materials by way of a computer-programmed robotic arm.
Alquist discovered some arduous classes through the undertaking in Iowa, together with the necessity for an R&D course of every time its tools is utilized in a brand new local weather, as temperature shifts may cause all types of points with the concrete.
“That is a part of the problem of introducing new know-how to the world,” stated Zack Mannheimer, Chairman and Founding father of Alquist 3D.
The corporate bumped into temperature points with the Walmart enlargement as nicely, as Tennessee will get sizzling and humid within the summertime. The workforce really wanted to chill down the overheating concrete with water so it will get again all the way down to the perfect temperature for printing. As well as, Alquist’s authentic pump was incompatible with the fabric, and a number of other hoses acquired clogged through the course of.
Alquist 3D CEO Patrick Callahan defined, “There’s quite a few issues that we’ve discovered.”
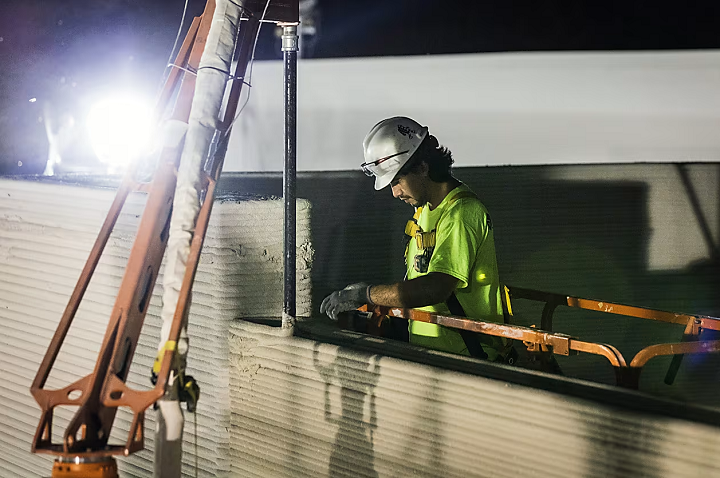
One employee is all the time positioned to carefully observe the robotic arm’s output and to verify the concrete is holding agency.
The undertaking was delayed a number of weeks as a result of aforementioned materials points, in addition to bother getting native constructing permits. However as time went on, issues grew to become simpler and extra environment friendly. Alquist labored with FMGI, a full-service common contractor that has accomplished many previous building tasks for Walmart. Darin Ross, FMGI’s CEO, stated this Walmart enlargement undertaking was a mix of his firm’s “conventional building guys” and Alquist’s “new know-how guys and gals.” By combining the digital know-how of 3D printing with the extra conventional subtractive strategies of building, the workforce efficiently accomplished the Walmart enlargement.
That’s one thing Stephan Mansour, a marketing consultant at Wohlers Associates who focuses on AC, touched on earlier this yr on the biannual ASTM F42/ISO TC 261 assembly. 3D printing is “not this revolutionary sort of instrument that’s going to make magic,” however relatively simply one other useful gizmo within the toolbox. Maybe sometime quickly, it gained’t be out of the atypical to see robotic AC programs on building websites subsequent to excavators and cranes.
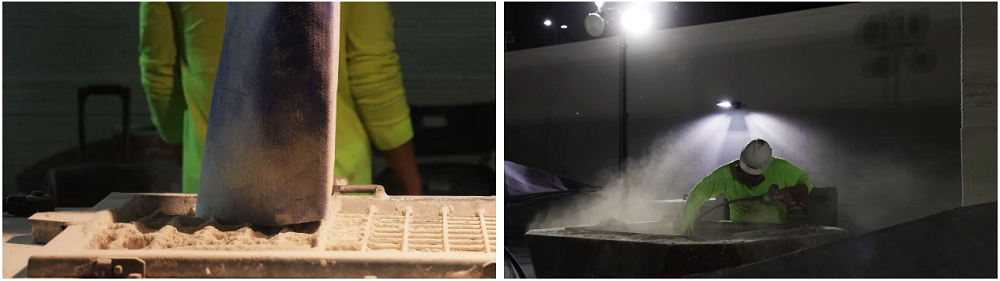
The Walmart job completed weeks delayed after building crews contended with finicky materials and clogged hoses.
There haven’t been too many CRE tasks accomplished with 3D printing, as a result of opposite to what’s been reported, the know-how isn’t all the time sooner or cheaper than conventional building. The Walmart undertaking didn’t end on schedule, and it was reported that the price of 3D printing the enlargement for the Tennessee retailer was about the identical as it will’ve been utilizing typical strategies. However, Walmart was apparently glad, because it’s already employed Alquist for one more related building undertaking. Walmart had $611.3 billion in income final yr, so lots is using on the corporate taking the teachings it’s discovered and making use of them.
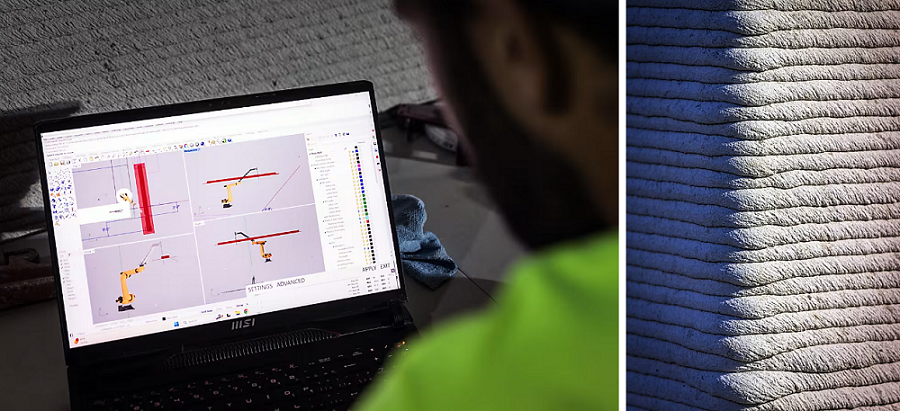
The development website in Tennessee blended ‘conventional building guys’ with tablet-toting, ‘new know-how guys and gals.’
Photos: Dustin Chambers for WSJ
Subscribe to Our E-mail Publication
Keep up-to-date on all the newest information from the 3D printing trade and obtain data and affords from third get together distributors.